The Ultimate Guide to Work Truck Trailer Welding Techniques Tips and Best Practices
Introduction
Work truck trailers play a crucial role in various industries, from transportation and construction to agriculture and landscaping. what is a tanker truck are relied upon to transport heavy loads, equipment, and materials safely and efficiently. However, the wear and tear of daily use can take a toll on work truck trailers, leading to issues that may compromise their structural integrity and overall performance. This is where welding comes into play.
Welding is a fundamental process in the maintenance and repair of work truck trailers. By utilizing the right techniques, tools, and materials, welders can effectively strengthen, repair, or fabricate components of these trailers to ensure they remain in optimal working condition. In this comprehensive guide, we will delve into the world of work truck trailer welding, exploring the various aspects of the process, from common challenges to best practices and everything in between.
1. Importance of Welding in Work Truck Trailer Maintenance
Work truck trailers are subjected to a wide range of environmental conditions and mechanical stresses during their operational lifespan. From exposure to harsh weather elements to the constant jostling and vibrations while on the road, these trailers face numerous challenges that can lead to structural damage and wear. Welding plays a critical role in addressing these issues by providing a reliable and durable method for repairing and reinforcing the trailer's components.
Proper welding techniques can help extend the lifespan of work truck trailers, reduce the risk of catastrophic failures, and ensure the safety of both the trailer operators and other road users. By understanding the importance of welding in work truck trailer maintenance, operators and maintenance personnel can take proactive measures to address potential issues before they escalate.
2. Common Welding Challenges in Work Truck Trailer Repair
While welding is an essential part of work truck trailer maintenance, it also presents its own set of challenges. Some of the common welding challenges faced in work truck trailer repair include:
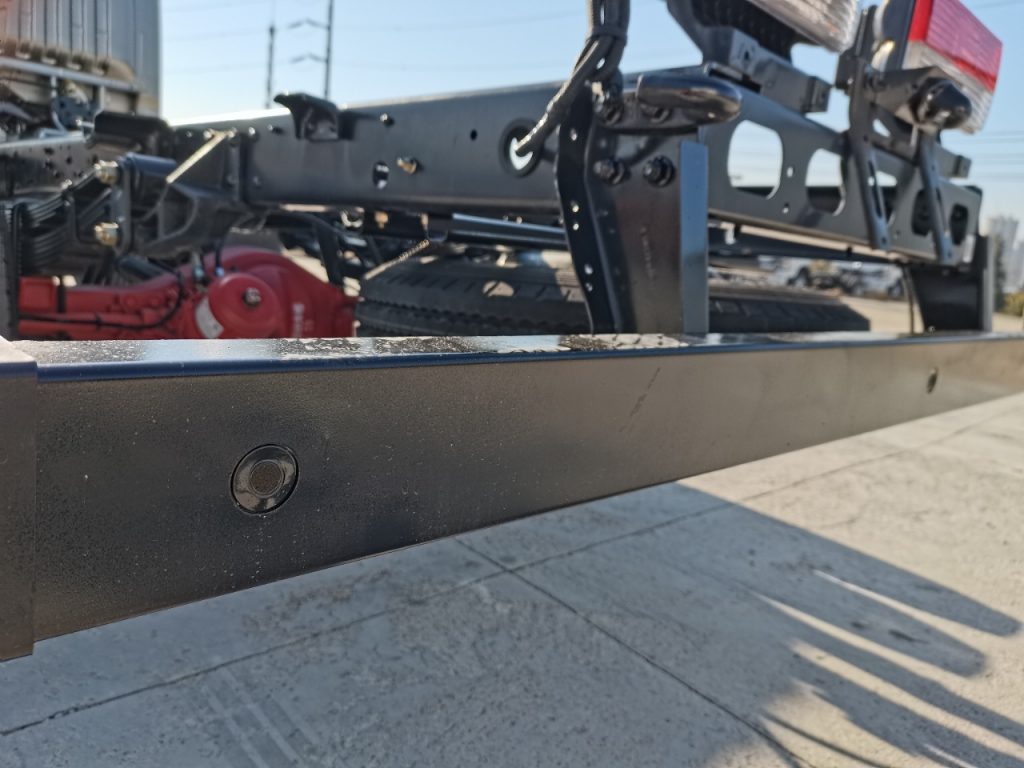
- Rust and corrosion: Work truck trailers are often exposed to moisture, road salt, and other corrosive substances that can lead to rust formation. Welding on corroded metal surfaces can be challenging as it may affect the quality and strength of the weld.
- Fatigue cracks: The constant stress and strain experienced by work truck trailers can result in fatigue cracks in critical components such as the trailer frame, hitch, and suspension. Welding these cracks requires careful preparation and execution to prevent further damage.
- Compatibility of materials: Work truck trailers are typically made from a combination of steel, aluminum, and other alloys. Welding different materials together can be complex and requires specialized techniques and filler materials to ensure a strong bond.
- Structural integrity: Maintaining the structural integrity of work truck trailers is paramount to their safe operation. Improper welding practices can compromise the trailer's strength and stability, leading to potential safety hazards.
By being aware of these common welding challenges, welders and maintenance personnel can adopt appropriate strategies and techniques to overcome them effectively.
3. Welding Techniques for Work Truck Trailer Repair
When it comes to welding work truck trailers, choosing the right welding technique is crucial to achieving strong and durable welds. The following are some of the common welding techniques used in work truck trailer repair:
- Shielded Metal Arc Welding (SMAW): Also known as stick welding, SMAW is a versatile and widely used welding process that is suitable for welding thick materials and outdoor applications. SMAW is ideal for repairing structural components of work truck trailers, such as frames and hitches.
- Gas Metal Arc Welding (GMAW): Commonly referred to as MIG welding, GMAW uses a wire electrode and a shielding gas to create a stable arc for welding. GMAW is well-suited for welding thin materials and provides high deposition rates, making it a popular choice for work truck trailer repairs.
- Flux-Cored Arc Welding (FCAW): FCAW is similar to GMAW but uses a tubular wire filled with flux to protect the weld pool from contaminants. FCAW is ideal for welding thick materials and is well-suited for outdoor welding applications where wind and drafts may affect the welding process.
- Gas Tungsten Arc Welding (GTAW): Also known as TIG welding, GTAW uses a non-consumable tungsten electrode and a shielding gas to create a precise and clean weld. GTAW is suitable for welding aluminum and stainless steel components of work truck trailers that require high-quality welds.
- Plasma Arc Welding (PAW): PAW is a high-precision welding process that utilizes a constricted arc and a shielding gas to create a focused and controlled weld. PAW is ideal for welding thin materials and intricate components of work truck trailers that require precise heat input.
By understanding the characteristics and applications of these welding techniques, welders can choose the most appropriate method for the specific requirements of work truck trailer repair.
4. Best Practices for Work Truck Trailer Welding
To ensure the success of work truck trailer welding projects, it is essential to follow best practices that promote safety, quality, and efficiency. The following are some key best practices for work truck trailer welding:
- Proper preparation: Before starting any welding work, thoroughly clean the surfaces to be welded to remove dirt, rust, paint, and other contaminants. Proper preparation ensures good weld penetration and adhesion, leading to strong and durable welds.
- Welding parameters: Adjust welding parameters such as voltage, current, travel speed, and shielding gas flow to suit the material thickness and type being welded. Proper welding parameters help prevent defects such as undercut, porosity, and lack of fusion.
- Joint design: Choose the appropriate joint design for the specific application and material being welded. Common joint designs for work truck trailer repair include butt joints, lap joints, and fillet welds. Ensure proper fit-up and alignment of the joint to achieve full weld penetration.
- Post-weld treatment: After welding, perform post-weld treatments such as grinding, cleaning, and stress relieving to remove weld spatter, smooth the weld profile, and reduce residual stresses. Proper post-weld treatment helps improve the aesthetics and durability of the weld.
- Inspection and testing: Inspect the completed welds visually and, if necessary, using non-destructive testing methods such as ultrasonic testing or magnetic particle inspection. Ensure that the welds meet the specified quality standards and structural requirements.
By adhering to these best practices, welders can enhance the quality and reliability of work truck trailer welding projects, leading to safe and long-lasting repairs.
5. Safety Considerations for Work Truck Trailer Welding
Safety should always be a top priority when performing welding on work truck trailers. Welding involves exposure to various hazards, including electrical shock, fumes, radiation, and fire, which can pose serious risks to the welder and others in the vicinity. To ensure a safe working environment, welders should observe the following safety considerations:
- Personal protective equipment: Wear appropriate personal protective equipment (PPE) such as welding helmets, gloves, safety glasses, and flame-resistant clothing to protect against burns, sparks, and arc flash.
- Ventilation: Ensure adequate ventilation in the welding area to remove welding fumes and gases that can be harmful if inhaled. Use exhaust fans or local exhaust systems to control airborne contaminants.
- Fire prevention: Keep a fire extinguisher nearby and be mindful of flammable materials in the welding area. Avoid welding near combustible materials and have fire safety measures in place to prevent accidents.
- Electrical safety: Inspect welding equipment regularly for damaged cables, frayed leads, and faulty connections. Use ground clamps and maintain a safe distance from live electrical components to prevent electrical shock.
- Training and supervision: Ensure that welders are properly trained and qualified to perform welding on work truck trailers. Provide supervision and guidance to inexperienced welders to prevent accidents and ensure the quality of the welds.
By prioritizing safety and implementing appropriate safety measures, welders can minimize the risks associated with work truck trailer welding and create a safe and healthy work environment.
6. Future Trends in Work Truck Trailer Welding
As technology continues to advance, the field of work truck trailer welding is also evolving to meet the changing demands of the industry. Some of the future trends in work truck trailer welding include:
- Automation: The use of robotic welding systems and automated welding equipment is becoming more prevalent in work truck trailer fabrication and repair. Automation increases productivity, precision, and repeatability, leading to higher quality welds and faster turnaround times.
- Advanced materials: The use of advanced materials such as high-strength steel, aluminum alloys, and composites in work truck trailer construction is driving the development of new welding techniques and processes. Welders will need to adapt to these materials and acquire the necessary skills to weld them effectively.
- Augmented reality: Augmented reality (AR) technology is being integrated into welding helmets and welding systems to provide real-time feedback and guidance to welders. AR technology enhances welder performance, improves weld quality, and reduces errors in work truck trailer welding.
- Sustainability: With a growing emphasis on sustainability and environmental responsibility, work truck trailer manufacturers are exploring eco-friendly welding processes and materials. Welding techniques that reduce energy consumption, emissions, and waste are gaining popularity in the industry.
By staying informed about these future trends and embracing innovation in work truck trailer welding, welders can stay ahead of the curve and maintain their competitiveness in the evolving landscape of the industry.
Conclusion
Work truck trailer welding is a critical aspect of maintaining the structural integrity, performance, and safety of these essential vehicles. By understanding the importance of welding in work truck trailer maintenance, addressing common welding challenges, employing suitable welding techniques, following best practices, prioritizing safety, and embracing future trends, welders can contribute to the longevity and reliability of work truck trailers across various industries.
This comprehensive guide has provided valuable insights into the world of work truck trailer welding, equipping welders, maintenance personnel, and industry professionals with the knowledge and skills needed to excel in this specialized field. By applying the principles and practices outlined in this guide, welders can ensure that work truck trailers continue to operate efficiently and safely, meeting the demands of today's dynamic work environments.